Traditional vs. Modern Metal Fabrication: What’s Changed Over the Years?
The metal fabrication industry has undergone significant transformations over the years, evolving from traditional handcrafting methods to high-tech, precision-driven processes. These changes have revolutionised how metal components are designed, produced, and used across various industries—from construction to aerospace and automotive.
In this post, we explore the key differences between traditional metal fabrication and modern techniques, and how innovations have shaped the industry in the UK. Whether you’re an industry professional, project manager, or simply curious about the evolution of fabrication, understanding these changes will help you appreciate the progress that has led to the advanced fabrication solutions available today.
At WORR Metal Fabrication, we embrace both traditional methods and modern innovations to deliver high-quality, cost-effective solutions tailored to our clients' needs.
Traditional Metal Fabrication: Handcrafting the Past
In the early days of metal fabrication, the process was a labour-intensive affair. Skilled craftsmen used basic tools and manual techniques to create metal components for a wide range of industries. The fabrication process involved cutting, welding, bending, and assembling metal pieces by hand.
Key Features of Traditional Fabrication:
Manual Labour-Intensive: Metalworkers relied heavily on their skills and experience, often using hand tools like hammers, anvils, and welding torches.
Fewer Customised Solutions: While traditional fabrication allowed for custom work, producing highly intricate designs was time-consuming and difficult.
Less Precision: With limited equipment, it was harder to achieve the level of accuracy and uniformity that modern techniques can provide.
Limited Scale: Traditional methods were often not suited for mass production, and fabrication was typically done on a smaller scale.
Challenges with Traditional Methods:
Time-Consuming: Fabricating components by hand often took longer, which could increase lead times for projects.
Higher Risk of Errors: With fewer tools to assist with accuracy, the likelihood of human error increased, potentially leading to costly mistakes.
Labour Costs: Traditional metalworking required a high degree of manual labour, which could be expensive over time.
Modern Metal Fabrication: The Era of Automation and Precision
Fast forward to today, and metal fabrication has entered a new era. Advanced machinery, automation, and cutting-edge technologies now drive the industry, allowing for faster production, greater accuracy, and more complex designs.
Key Features of Modern Fabrication:
Automation and Robotics: Modern metal fabrication facilities use robotic arms and automated systems for processes like welding, cutting, and bending. These technologies allow for faster production cycles and consistent quality.
Advanced Software: Computer-Aided Design (CAD) and Computer-Aided Manufacturing (CAM) software enable designers to create complex parts with greater precision and fewer errors.
3D Printing and Additive Manufacturing: Metal 3D printing allows for rapid prototyping and small-batch production of intricate components that were once impossible to make with traditional methods.
Precision Engineering: Modern machines like laser cutters, plasma cutters, and CNC (Computer Numerical Control) machines allow for incredible accuracy, reducing material waste and improving efficiency.
Advantages of Modern Methods:
Speed and Efficiency: Automated processes drastically reduce production time, allowing for quicker turnaround on large orders.
High Precision: CNC machines and 3D printers can achieve micrometer-level accuracy, ensuring that parts fit perfectly with minimal adjustments.
Cost Savings: While the initial investment in equipment may be high, modern techniques reduce long-term labour and material costs, as well as the potential for errors.
Scalability: Modern fabrication methods are ideal for both small and large-scale projects, allowing manufacturers to handle high-volume production efficiently.
Emerging Trends in Modern Fabrication:
Sustainability Focus: Modern fabrication has placed a greater emphasis on eco-friendly processes, such as recycled materials, energy-efficient machinery, and low-waste production methods.
Smart Factories: The integration of Internet of Things (IoT) devices and real-time data monitoring has led to the creation of “smart factories” that optimise performance and reduce downtime.
Customization: Advanced technology enables highly customisable products with minimal lead time, which is particularly beneficial in industries like aerospace, automotive, and renewable energy.
The Evolution of Metal Fabrication: A UK Perspective
The UK has been at the forefront of the metal fabrication revolution. From the industrial revolution to the rise of automation in the late 20th and early 21st centuries, UK manufacturers have continually adapted to new technologies and methodologies.
Key Industry Shifts in the UK:
From Manual Labour to Robotics: The shift from manual, labour-intensive fabrication to automated, robotic-driven processes has allowed UK fabricators to stay competitive in global markets.
Rise of Digital Fabrication: UK companies are now using 3D printing, laser cutting, and CNC machining for more precise and efficient metalworking. These technologies have transformed sectors such as aerospace, automotive, and renewable energy.
Commitment to Sustainability: With a growing focus on sustainability, UK fabricators are investing in green technologies and adopting low-waste production techniques in line with the country’s net-zero goals by 2050.
WORR Metal Fabrication is proud to be part of this transformation, offering cutting-edge fabrication services and embracing both traditional and modern techniques to meet the demands of today’s industries.
Traditional vs. Modern Fabrication: Which Is Best?
Both traditional and modern metal fabrication methods have their place in today’s industry. Traditional methods are still valued for their craftsmanship and ability to handle small-scale, intricate projects. However, modern fabrication techniques have become the go-to for high-precision, high-volume, and time-sensitive production.
For many projects, the combination of traditional techniques for custom work and modern methods for speed, efficiency, and precision provides the best of both worlds.
Conclusion: The Future of Metal Fabrication
As technology continues to advance, metal fabrication will only become more efficient, precise, and sustainable. The UK’s metal fabrication industry is poised to embrace future innovations, and at WORR Metal Fabrication, we’re committed to staying ahead of the curve.
Whether your project requires traditional craftsmanship or the latest automated techniques, we have the expertise to bring your ideas to life. Contact us today to learn how we can help with your next metal fabrication project.




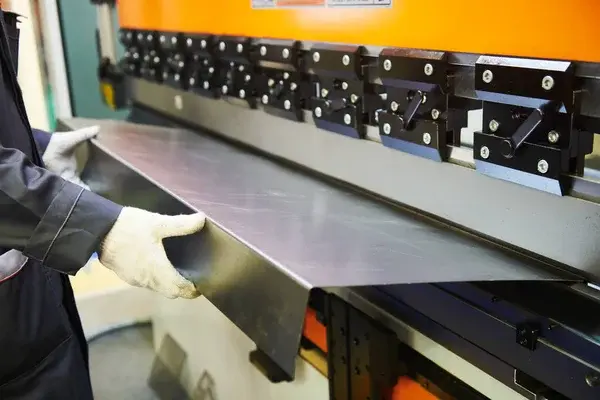
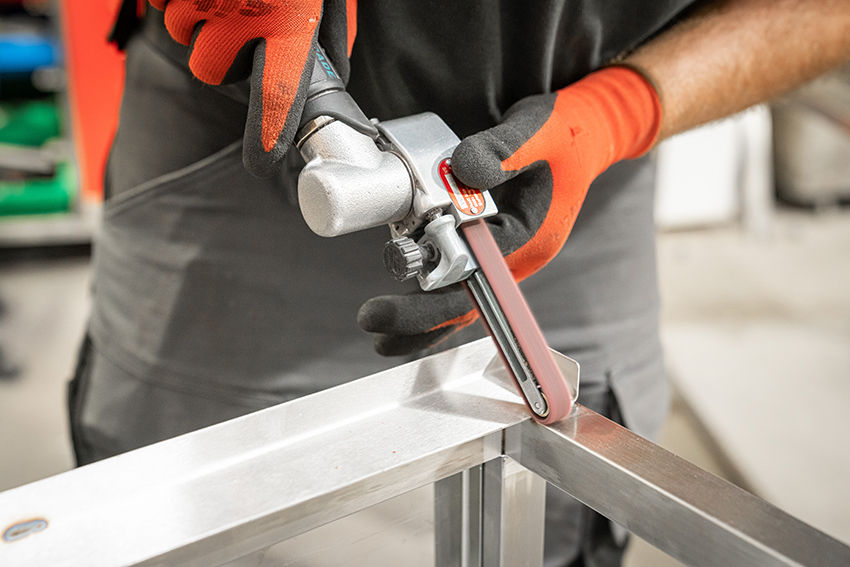

Comentários